حکاکی لیزری بهعنوان یکی از فناوریهای پیشرفته و دقیق در فرآیندهای تولید صنعتی شناخته میشود. این فناوری در صنایع مختلفی نظیر خودروسازی، الکترونیک، پزشکی، تبلیغات و دکوراسیون مورد استفاده قرار میگیرد. یکی از ویژگیهای اصلی حکاکی لیزری، امکان ایجاد الگوها و طرحهای بسیار دقیق و تکرارپذیر بر روی سطوح مختلف است؛ اما آنچه که در بسیاری از پروژهها نادیده گرفته میشود، نقش حیاتی نوع متریال در تعیین کیفیت و دقت نهایی حکاکی است.
نوع مادهای که حکاکی روی آن انجام میشود، تعیینکنندهی پارامترهایی از جمله میزان جذب انرژی لیزر، نوع واکنش حرارتی، احتمال ایجاد تغییر رنگ، ایجاد دوده، عمق نفوذ، وضوح خطوط و حتی دوام حکاکی در برابر سایش است. بهعبارتدیگر، لیزر بهتنهایی تعیینکننده کیفیت نهایی نیست؛ بلکه خواص ذاتی متریال نقش مکملی بسیار مهم دارند.
در این مقاله بهطور جامع تأثیر ویژگیهای فیزیکی، شیمیایی و ساختاری متریالهای مختلف بر فرآیند حکاکی لیزری مورد بررسی قرار خواهد گرفت. ابتدا مروری بر اصول حکاکی لیزری انجام میشود، سپس ویژگیهای کلیدی متریالها بررسی شده و عملکرد لیزر بر انواع مواد مورد مقایسه قرار میگیرد. همچنین راهکارهایی برای بهینهسازی فرآیند حکاکی در مواجهه با چالشهای متریالی ارائه خواهد شد تا تولیدکنندگان بتوانند با دقت بیشتری تجهیزات، تنظیمات و مواد اولیه خود را انتخاب کنند.
مروری بر فناوری حکاکی لیزری
حکاکی لیزری فرآیندی است که در آن پرتوی متمرکز شدهی نور لیزر با توان بالا به سطح یک ماده برخورد میکند و باعث تبخیر، ذوب یا تغییر شیمیایی در ناحیهی مورد نظر میشود. بسته به نوع لیزر و پارامترهای عملیاتی، این تغییر میتواند بهصورت یک علامت سطحی یا یک فرورفتگی دائمی بر روی سطح باقی بماند. از مهمترین انواع لیزر مورد استفاده میتوان به لیزرهای CO2، فایبر، Nd:YAG و لیزرهای UV اشاره کرد.
لیزر CO2 با طول موج ۱۰.۶ میکرومتر برای حکاکی روی موادی چون چوب، شیشه، پلاستیک و پارچه مناسب است. این نوع لیزر جذب بالایی در مواد غیرفلزی دارد. در مقابل، لیزرهای فایبر که دارای طول موج کوتاهتر (حدود ۱.۰۶ میکرومتر) هستند، برای حکاکی بر روی فلزات بسیار مؤثرند؛ زیرا فلزات انرژی این لیزرها را بهتر جذب میکنند.
در فرآیند حکاکی لیزری، متغیرهایی مانند توان لیزر، فرکانس پالس، مدت زمان تابش، سرعت حرکت هد لیزر، ضخامت متریال و نوع سطح آن تأثیر مستقیم بر کیفیت حکاکی دارند. افزایش توان خروجی باعث افزایش عمق حکاکی میشود، اما میتواند منجر به سوختگی یا ذوب بیشازحد شود. کاهش سرعت اسکن، مدت زمان بیشتری را به انرژیدهی اختصاص میدهد که برای مواد سخت مناسب است.
این فناوری به علت مزایایی چون عدم نیاز به تماس مستقیم، دقت بالا، سرعت زیاد و عدم تولید ضایعات مکانیکی، به یکی از روشهای ترجیحی حکاکی در تولید صنعتی تبدیل شده است
خواص فیزیکی و شیمیایی متریالها و تأثیر آنها بر عملکرد لیزر
یکی از عوامل حیاتی در تعیین کیفیت حکاکی لیزری، خواص فیزیکی و شیمیایی متریالی است که حکاکی بر روی آن انجام میشود. این خواص بهطور مستقیم بر نحوه جذب انرژی لیزر، نوع برهمکنش حرارتی، و در نهایت شکل، عمق، وضوح و دوام حکاکی تأثیر میگذارند.
۱. رسانایی حرارتی: موادی مانند آلومینیوم یا مس دارای رسانایی حرارتی بالا هستند. در این مواد، گرمای تولید شده توسط لیزر به سرعت در ماده پخش میشود و در نتیجه تمرکز گرما در نقطهی حکاکی کاهش مییابد. این مسئله باعث میشود که عمق حکاکی کاهش یابد یا نیاز به افزایش توان لیزر باشد. در مقابل، موادی مانند چوب یا پلاستیک که رسانایی حرارتی کمی دارند، گرما را حفظ میکنند و در نتیجه حکاکی با عمق بیشتر و سرعت بالا قابل اجرا است.
۲. بازتابندگی سطح: سطوح براق و فلزات صیقلی (مانند طلا، نقره یا فولاد ضدزنگ) میزان زیادی از نور لیزر را بازتاب میدهند. بازتابش باعث کاهش انرژی مؤثر وارد شده به سطح ماده میشود. در این حالت، بهرهوری حکاکی کاهش مییابد و ممکن است نیاز به پوشش دادن سطح یا استفاده از لیزرهایی با طول موج متفاوت باشد.
۳. نقطه ذوب و دمای تبخیر: این ویژگیها تعیین میکنند که چه مقدار انرژی برای تغییر شکل سطح ماده لازم است. موادی با نقطه ذوب پایینتر، زودتر به تغییرات حرارتی پاسخ میدهند. پلاستیکها در این زمینه واکنش سریعی دارند، در حالی که فلزات سنگین مانند تیتانیوم نیازمند انرژی بیشتری هستند.
۴. ترکیب شیمیایی و افزودنیها: وجود مواد افزودنی مانند رنگدانهها، رزینها یا پوششهای سطحی میتواند باعث بروز واکنشهای شیمیایی ناخواسته، دودهای سمی یا تغییر رنگ در محل حکاکی شود.
۵. ساختار مولکولی و چگالی: موادی با ساختار متراکمتر معمولاً سختتر در برابر نفوذ لیزر مقاومت میکنند، اما در عوض خطوط دقیقتری را ایجاد میکنند.
درک این ویژگیها برای انتخاب نوع لیزر مناسب، تنظیمات بهینه و جلوگیری از نقصهای سطحی مانند سوختگی، دود گرفتگی یا تغییر رنگ، بسیار ضروری است.

مقایسه عملکرد لیزر بر انواع متریالها (فلز، چوب، پلاستیک، شیشه و ...)
در فرآیند حکاکی لیزری، نوع متریال تأثیر زیادی بر کیفیت و جزئیات خروجی دارد. در ادامه به بررسی عملکرد لیزر بر روی برخی از رایجترین متریالها میپردازیم:
۱. فلزات: حکاکی بر روی فلزات نیازمند لیزرهایی با توان بالا (مانند فایبر لیزر یا Nd:YAG) است. فلزات دارای بازتابندگی بالا، نقطه ذوب بالا و رسانایی حرارتی قوی هستند که فرآیند را پیچیده میسازد. برای مثال، آلومینیوم نیازمند تنظیم دقیق پارامترهاست تا از ذوب سطحی و خطای حرارتی جلوگیری شود. در مقابل، فولاد ضد زنگ نتیجهی واضحتری دارد.
۲. چوب: چوب به دلیل ماهیت آلی، جذب انرژی بالایی دارد و به سرعت دچار سوختگی یا تغییر رنگ میشود. با لیزر CO2 میتوان طرحهای بسیار ظریف و زیبا بر روی چوب ایجاد کرد. با این حال، رطوبت موجود در چوب و نوع بافت آن ممکن است منجر به تفاوت در عمق حکاکی شود.
۳. پلاستیکها: بسیاری از پلاستیکها (مانند ABS، پلیکربنات، پلیاتیلن) در مقابل لیزر به خوبی واکنش میدهند. با این حال، ممکن است تولید دود یا گاز سمی در فرآیند وجود داشته باشد. برخی پلاستیکها در اثر حرارت تغییر رنگ میدهند که میتواند مفید یا مشکلساز باشد.
۴. شیشه: شیشه بسیار شکننده و حساس به تغییرات حرارتی است. استفاده از لیزرهای UV یا CO2 پالسی، برای جلوگیری از ترک خوردگی و ایجاد لایهبرداری سطحی، رایج است. استفاده از اسپری یا پوشش جاذب لیزر نیز برای بهبود نتیجه مفید است.
۵. پارچه و چرم: پارچهها معمولاً نازک هستند و با لیزر CO2 به خوبی حکاکی میشوند. تنظیم توان بسیار پایین برای جلوگیری از سوختگی ضروری است. چرم طبیعی نیز واکنش خوبی به حکاکی دارد و میتوان طرحهای دقیق بر آن ایجاد کرد.
این مقایسه نشان میدهد که هر متریال به تنظیمات خاصی از جمله توان، سرعت اسکن، فرکانس و نوع لیزر نیاز دارد و استانداردسازی این پارامترها برای تضمین کیفیت امری ضروری است
چالشهای متریالی در حکاکی لیزری
حکاکی لیزری علیرغم دقت بالا، در مواجهه با انواع متریالها با چالشهایی روبهروست که در صورت عدم مدیریت مناسب میتواند منجر به کاهش کیفیت محصول نهایی شود.
۱. سوختگی بیشازحد: موادی مانند چوب یا چرم در برابر انرژی حرارتی بسیار حساس هستند. افزایش توان یا کاهش بیشازحد سرعت حرکت میتواند منجر به سوختگی ناخواسته شود که ظاهر کار را خراب میکند.
۲. دود و بخارات سمی: برخی مواد شیمیایی مانند PVC یا پلیاستر در اثر حرارت گازهای خطرناک تولید میکنند. این گازها هم برای اپراتور خطرناک هستند و هم باعث آلودگی لنز و افت کیفیت حکاکی میشوند.
۳. ناهمگنی سطح متریال: موادی که سطح یکنواختی ندارند (مانند چوب با گرههای طبیعی یا چرم با منافذ متغیر) باعث ایجاد تغییرات غیرقابل پیشبینی در شدت حکاکی میشوند.
۴. انعکاس بالا در فلزات: لیزر ممکن است بازتاب شود و منجر به آسیب دستگاه یا کاهش دقت شود. استفاده از پوششهای ضد بازتاب یا لیزرهای خاص برای کاهش این اثر ضروری است.
۵. ترک خوردگی در شیشه و سرامیک: این مواد شکننده در صورت عدم تنظیم صحیح فرکانس پالس یا سرعت تابش، دچار ترک یا شکست میشوند.
درک این چالشها و اتخاذ تمهیدات مناسب (مانند تهویه مناسب، استفاده از ماسک فیلتر دار، تنظیمات دقیق، استفاده از افزونههای نرمافزاری تنظیم توان خودکار) برای افزایش ایمنی و کیفیت الزامی است
راهکارهای بهینهسازی حکاکی بر اساس نوع متریال
برای دستیابی به حکاکی لیزری دقیق، یکنواخت و با کیفیت بالا، اتخاذ راهکارهای تخصصی متناسب با نوع متریال ضروری است:
– فلزات: استفاده از فایبر لیزر با تنظیمات قدرت بالا، فرکانس پالس پایین و استفاده از پوششهای کاهشدهنده بازتاب مانند رنگهای مات قبل از حکاکی.
– چوب: استفاده از توان متوسط، سرعت بالاتر و جلوگیری از تمرکز بیشازحد انرژی در یک نقطه؛ خشک بودن کامل چوب نیز توصیه میشود.
– پلاستیکها: شناخت ترکیب شیمیایی ماده برای جلوگیری از گازهای سمی، استفاده از تهویه صنعتی و فیلترهای جذبکننده دود.
– شیشه: استفاده از پوشش مات یا اسپری جاذب لیزر، انتخاب لیزر پالسی با انرژی پایین و خنککاری سطح.
– مواد مرکب یا چندلایه: تست اولیه بر نمونههای مشابه، استفاده از نرمافزارهای تنظیم دینامیک توان و اسکن چند مرحلهای برای کاهش فشار حرارتی.
همچنین استفاده از نرمافزارهای هوشمند CAD/CAM که امکان تنظیم خودکار پارامترها را براساس نوع متریال دارند، میتواند موجب افزایش بهرهوری و کاهش خطاهای انسانی شود
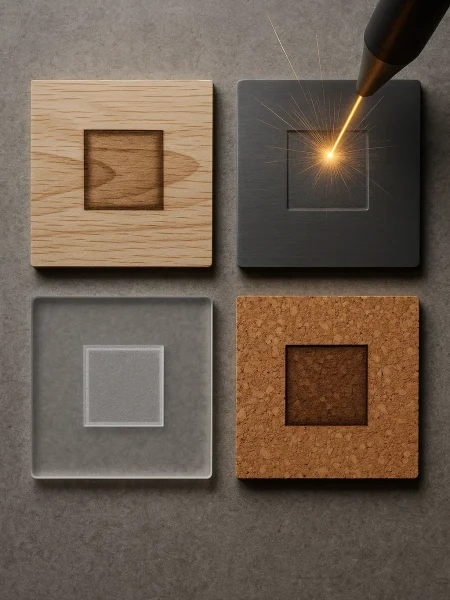
انتخاب صحیح متریال و درک عمیق از خصوصیات آن، یکی از ارکان موفقیت در حکاکی لیزری با کیفیت بالا بهشمار میرود. هر ماده دارای ویژگیهایی است که باید در فرآیند تنظیم پارامترهای لیزر لحاظ شوند. از رسانایی حرارتی و بازتابندگی گرفته تا واکنشهای شیمیایی سطحی، همگی در شکلگیری نتیجه نهایی تأثیرگذار هستند.
با توسعه فناوری، امکان شخصیسازی تنظیمات حکاکی برای انواع مواد فراهم شده است؛ اما همچنان شناخت عملی و تجربی از رفتار متریالها در برابر تابش لیزر اهمیت حیاتی دارد. تولیدکنندگان و اپراتورها باید با انجام تستهای اولیه، استفاده از دستورالعملهای فنی و بهرهگیری از دادههای علمی، فرآیند حکاکی را بهینهسازی کرده و به دقت و کیفیت مطلوب دست یابند.
در نهایت، مزیت اصلی حکاکی لیزری یعنی دقت بالا و قابلیت شخصیسازی، تنها در صورتی محقق خواهد شد که متریال، فناوری و تنظیمات بهدرستی با یکدیگر هماهنگ شوند.